Tungsten Coating On Twin-screw and Barrel Sets
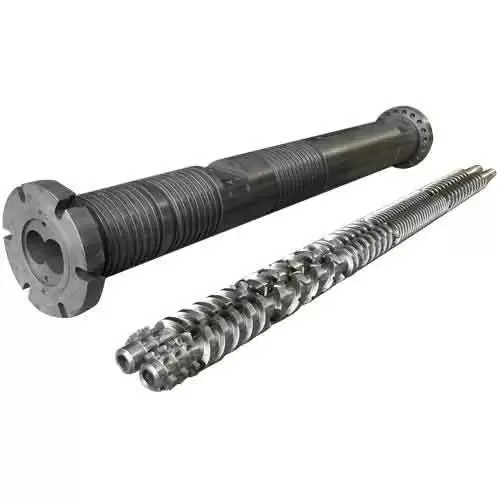
In polymer and copolymer production, both of tungsten coating serve a purpose on twin-screw and barrel sets, particularly in combining and conversion procedures. Tungsten compounds improve these important processing machinery components' lifespan, durability, wear resistance, & performance in general.
Tungsten has become famous for exhibiting outstanding durability and hardness. Tungsten coatings might extend the service life of twin screws and barrels by minimizing degradation imposed on by the aggressive qualities of plastic manufacturing. This might boost the product's resilience and durability. Greater durability to wear has the potential to boost processing efficiency and effectiveness. As time passes, more frequent and improved quality production may be the consequence of fewer nicks on the barrels and screws. Since tungsten coatings involve fewer fixes for substitutions, they can help maximize profitability. As a result, their is less maintenance and the manufacture process can simpler and more continual.
Tungsten Coating On Twin-screw and Barrel Sets Advantages
Generally, overall, tungsten coatings function nicely with a variety of materials and polymers that have been synthesized when extruded. Owing to their versatility, tungsten-coated elements could be used in several different sectors, among them copolymer thinking about, rubber's buoyant and resins. More fluid surface finishes may be produced with tungsten coatings, which may be advantageous in some processing scenarios. Enhanced material flow, lower friction, and higher overall extrusion or combining process effectiveness are all factors that can be credited to a nicer surface. Since it has high thermal conductivity, tungsten may be useful in situations where heat transmission is essential. It contributes to consistent material attributes by preserving the device's heat constant overall.
Tungsten Coating with HVOF gun Working
Utilizing a High-Velocity Oxygen Fuel (HVOF) gun for covering germanium needs a thermal spray conduct that provides a heavy, excellent coat with exceptional substrate compliance. HVOF has become a commonly utilized tungsten coating application process because it produces a coating with outstanding bond power, excellent hardness, and minimal permeability.
Before to beginning the spraying procedure that's the substrate—such as the twin-screw or barrel set—must be thoroughly cleaned and prepped. typically, this involves washing thoroughly to eliminate any potential impurities, oxides, or other residues that might interfere with the tungsten coating's capability to adhere to the substrate. To safeguard them throughout the sprayed process, regions of the surface that ought not receive the tungsten coating could have to be shielded by masks. The following allows accurate coating application. The HVOF spray gun has been set up and tweaked. In general, small amounts of tungsten powder is inserted into the a gun, where it is incorporated with oxygen that moves rapidly when detonated. Following the general direction of the substrate present, which produces a hypersonic fireball.
As the tungsten flakes comes onto encounter to the substrate, their instantly become cold and harden. The granules' rapid motion encourages the growth of an in thickness tightly-bonded covering. The surface of the substrate is made to resist the heat shock encountered with that process. It might need many strokes to get an appropriate coating density. Tungsten gets applied in strata on every pass, and this process is carried out until the needed coating thickness is reached. Upon the application of the tungsten coating, post-coating treatments can be carried out to improve certain characteristics or relieve any persisting tensions. The mechanical characteristics of the coating can be improved by using heat treatment or different processes.
Tungsten Coating in India
We offer an established brand among the Indian HVOF Coating company operations. We are an exceptional HVOF gun manufacture and supplier, having all the complexities covered. For applying an HVOF coatings to workpieces that are additionally, we deliver tungsten powder including every other needed HVOF gun attachments. Our HVOF coatings deliver a remarkable resistance to wear, preserving the barrel from twin screw areas from erosion and scratches. This is particularly valuable in situations when the elements have been exposed to chemicals and difficult operating environments. The additional wear protection of twin screws and barrels contributes to a longer lifespan. Given that components that have been treated have become more resilient to the demands of ongoing operations, this will lead to a verified and dignitary establishment of existing amenity.